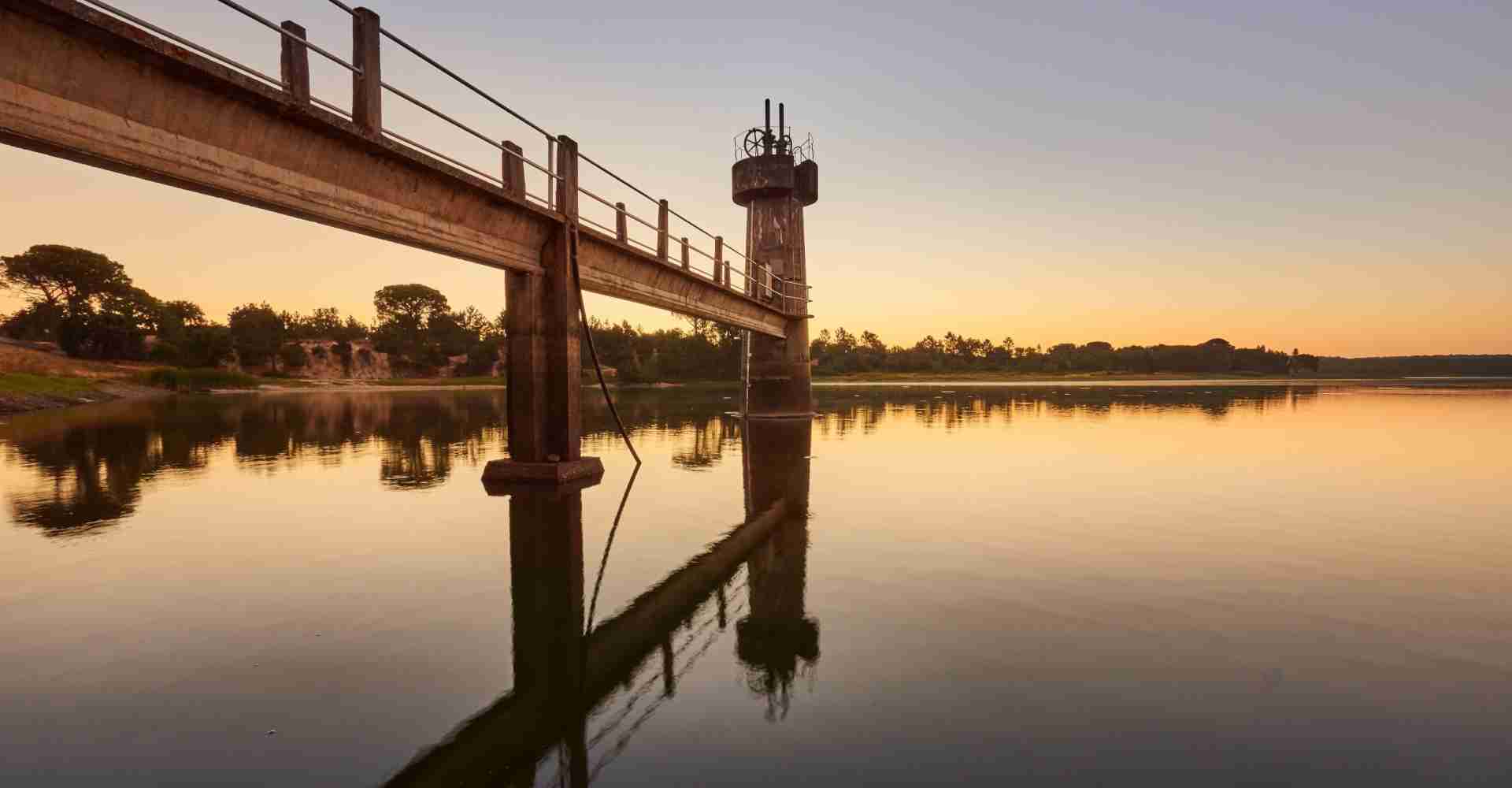
WHY VOLUMETRIC MIXERS ARE YOUR FIRST CHOICE FOR POURING INTAKE STRUCTURES
WHY VOLUMETRIC MIXERS ARE YOUR FIRST CHOICE FOR POURING INTAKE STRUCTURES
Water intake structures are among the most important concrete projects. Though rarely seen by the public, they build a bridge between a water source and other components of the water supply system. Without a solidly constructed intake, consumers may have no reliable water supply. Volumetric concrete mixers are the perfect tool for these crucial projects.
WHAT INTAKE STRUCTURES HAVE TO WITHSTAND
Pouring water intakes requires precisely mixed concrete available exactly when it is needed. This high-quality concrete is the only way to ensure that the intake structure can withstand the demands put on it.
Water intakes have to resist several environmental forces starting with the water pressure itself. They also have to be strong enough to withstand waves, strong winds, fast-flowing floating debris, geological formations, and annual rainfall. Controlling or limiting erosion, removing solids, and minimizing turbulence in the water flow are key considerations for intake design and construction. Taking all those factors into consideration, water intakes are generally placed in the purest zone of the water source.
Depending on the exact conditions in the respective location, water intakes often require specific concrete mixes in large quantities. Because of those specific requirements, volumetric mixers are the perfect solution for pouring water intakes.
TYPES OF INTAKE STRUCTURES
Although each water intake pour will be slightly different, structures generally fall into one of four types. In some cases, a project may fall into more than one of those categories.
1. EXPOSED INTAKE
Exposed water intakes usually come in the form of water towers. They have become very common because they are easy to operate. Water towers allow the operators to accommodate a wide fluctuation in the supply’s water level. They also make it possible to remove water from greater depths. Depending on the water level, towers usually have multiple intake ports at different heights.
2. WET INTAKE
In a wet intake design, the water tower is filled to the same level as the sources of the supply. The water initially filters through penstocks before it enters the tower. From there, it is pumped to the water treatment plant.
3. DRY INTAKE
With this type of design, the water tower does not hold any water. Instead, it houses conveying pipes that carry the water directly from the source to the treatment plant. The tower itself is accessible for operations, maintenance, and adjustments.
4. SUBMERGED INTAKE
Submerged intakes are among the most challenging to pour as the entire system is constructed underwater. They are often the best choice for water supplies from lakes or rivers. The intake channel is placed below the bed of the lake or river from which only the inlet end protrudes.
These constructions have a few advantages when it comes to dealing with environmental factors. They hardly disturb the flow of the water in rivers. It is almost impossible for floating debris to compromise the intake. Plus, in colder regions, ice forming on the surface of the lake or river rarely causes anything other than minimal issues.
ADVANTAGES OF VOLUMETRIC MIXERS FOR WATER INTAKES
Volumetric concrete mixers have several advantages over traditional mixers in the construction of water intakes.
- Remote Locations
- Adjustable Mix Design
- High-Performance Concrete
REMOTE LOCATIONS
Water sources and water intake construction projects tend to be in remote locations. Whilst those pose difficulties for traditional barrel mixers, volumetric mixers can easily rise to the challenge.
Mobile concrete mixers travel to where you need them to be. To keep them running for the duration of the pour, project managers only need to ensure a sufficient supply of cement and aggregates for the mixers to be ready to supply the amount of concrete necessary. Because it is mixed on-site, the concrete will have the right consistency for the project.
In remote locations, volumetric mixers help avoid delays during the project. There is no need to wait for a truck that has got stuck in traffic, for example. In addition, you are able to pour fresh concrete, ensuring the pour is of the highest possible quality. If mixer trucks have to travel a long distance from the batch plant to the pouring site, the quality of the mix deteriorates. Once at the site, water may need to be added which changes the strength of the finished concrete.
Volumetric mixers are ready to pour when you need them. You are not wasting any concrete if you need less than initially thought, and there are no delays in case you need to mix more.
ADJUSTABLE MIX DESIGN
Volumetric mixers allow you to change the mix on the spot.
As the project’s requirements change, your operator simply adjusts the desired mix on the touchpad of the Commander control system, and the mixer starts pouring the new design. There is no need for separate mixer trucks or repeated trips to the batch plant. It’s a much more effective use of time and equipment compared to traditional mixers and allows operators to adapt to the changing needs of the project.
HIGH-PERFORMANCE CONCRETE
Submerged water intakes require you to pour underwater concrete (UWC). This is a high-performance concrete that needs to be strong enough to resist the water pressure around it. With other types of water intakes, concrete may be partially submerged.
UWC needs to build up viscosity quickly during the mixing process. It also needs to be highly flowable and consolidate itself. Having your mixer on-site and being able to control the mix in real-time is a distinct advantage of volumetric mixers.
Whilst the specific mix rarely needs to be adjusted during the pour, having the option to adjust it helps ensure the best possible outcome.
Volumetric concrete mixers are the perfect tool for pouring water intake structures. They perform in remote locations, allow on-site adjustment of mix and quantity, and help you save time and resources throughout the entire project. Their flexibility allows you to accommodate any type of water intake and deliver the exact mix required, every time.