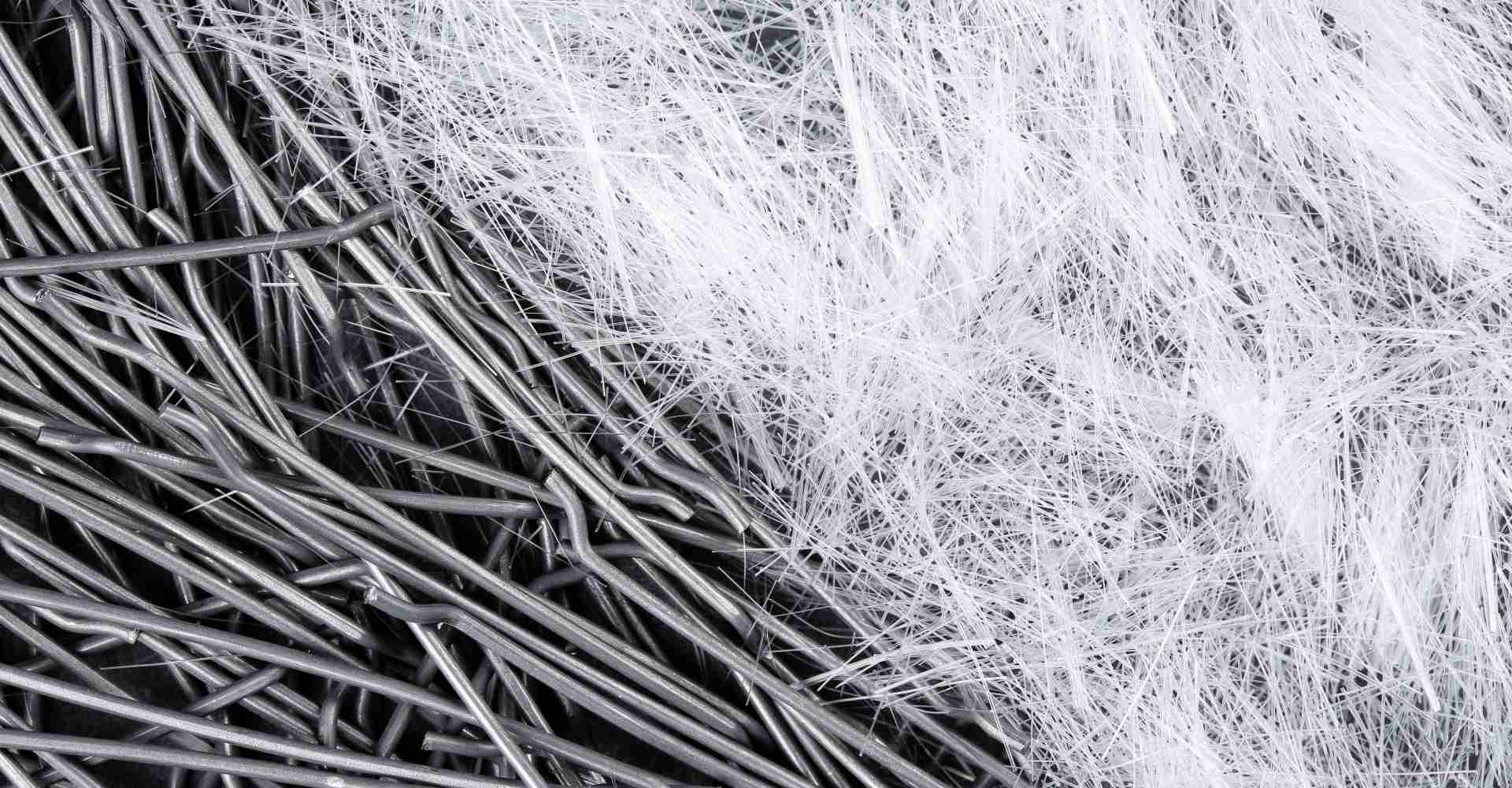
WHAT IS FIBER-REINFORCED CONCRETE?
WHAT IS FIBER-REINFORCED CONCRETE?
Concrete is one of the most versatile building materials construction contractors can choose. One of the reasons behind this versatility is the fact that it can be combined with other components to create a stronger compound. One example of such a compound is fiber-reinforced concrete (FRC). Here is everything you need to know.
A BIT OF BACKGROUND ON FIBER-REINFORCED CONCRETE
According to the American Concrete Institute, FRC is a type of concrete that contains “dispersed, randomly oriented fibers.” This variety of concrete is made from cement, aggregate, water, and discrete reinforcing fibers.
The concrete base used for FRC can either be a standard mix or one that has been specifically created for certain applications. As a construction contractor, you may choose fiber-reinforced concrete for projects that require long-term serviceability of the final structure.
Builders have used fibers to reinforce building materials for centuries, long before concrete became popular. Horsehair was one of the favorites in the past. Combined with straw, it helped make mudbricks stronger. Around 1900, contractors started adding asbestos to concrete to make it stronger. Once scientists discovered the health risks associated with asbestos, the industry needed to find a replacement.
Roughly at the same time, in the 1950s, engineers became interested in composite materials. That is when FRC first became an area of interest. About a decade later, contractors had begun reinforcing concrete with synthetic materials, steel, and glass. Today, contractors can choose between a wider range of reinforcement materials. Nonetheless, research continues to find the ideal compound.
WHY USE FIBER-REINFORCED CONCRETE?
Fiber-reinforced concrete helps control cracking, which is likely to occur due to plastic and drying shrinkage. That is one of the reasons behind its growing popularity. Subject to the type of fiber chosen for the compound, it can increase toughness ten to 40 times.
Other advantages include the ability to add high tensile strength when other reinforcements such as steel rebar are not suitable. FRC can resist greater strain than regular concrete as well as improve the durability of the concrete.
In areas with challenging weather conditions, reinforced concrete displays greater resistance to repeated freezing and thawing. Depending on your project, fiber-based reinforcement may be enough, removing the need for steel reinforcement.
CHOOSING THE RIGHT TYPE OF FIBER
The characteristics of the final fiber-reinforced concrete depend on several factors:
- The ratio of water to cement
- Percentage of fibers
- Length and diameter of the chosen fibers
Here is an overview of commonly used types of fiber for concrete reinforcement.
1. POLYPROPYLENE FIBERS
Polypropylene is a synthetic fiber, transformed from propylene. When it is used as a reinforcing fiber in concrete, it helps control cracking and reduces the permeability of concrete as well as the bleeding of water.
Polypropylene is a white material with high levels of resistance to acids, alkalis, and organic solvents. It is the only type of fiber used in volumetric mixers to date.
2. POLYESTER FIBERS
Polyester fiber-reinforced concrete is a popular material for warehouse floors and other industrial floors as well as pavements and overlays. This is due to its superior resistance to cracks resulting from plastic shrinkage.
These fibers can also increase the concrete mix’s toughness and even its structural capacity.
3. STEEL FIBERS
As a metal reinforcement, steel fiber in concrete can change the material’s physical properties. Benefits include increased resistance to impact, cracking, material fatigue, and bending. Different types of steel fibers can increase durability and tenacity, which is why they are used in bridges, tunnels, and heavy-duty pavements, for example.
4. GLASS FIBERS
Glass fibers are extremely fine fibers. Their properties can be compared to polymers and carbon fibers, although they are less brittle than carbon fibers and much cheaper. They form very strong but relatively lightweight composites.
5. CARBON FIBERS
The advantages of carbon fibers include high tensile strength and stiffness as well as low weight. They tolerate extreme temperatures without noticeable thermal extension and are able to resist chemicals.
Which type of fiber you choose will depend on the specifications of your client’s requirements.
USING FIBER-REINFORCED CONCRETE WITH VOLUMETRIC MIXERS
In the past, producing fiber-reinforced concrete with volumetric mixers has been difficult. This was due to a lack of an automated system as adding fibers to your concrete mix simply does not work.
As a result, contractors using volumetric mixers were losing out to companies operating Ready-mix trucks.
Those difficulties have been overcome thanks to engineering developments like the ProAll fiber feeder. The fiber feeder is an add-on that is available for all ProAll Reimer mixers. It is easy to install and operate and allows contractors to combine the benefits and versatility of mobile volumetric mixers and fiber-reinforced concrete.
The fiber is chopped and dropped directly onto the belt to be mixed with other components. Automation makes this process easy and ensures that the fiber is fed at an even rate, cut accurately, and distributed evenly throughout the entire mix.
By adding the fiber feeder to your new or existing volumetric mixer, your construction business gains a competitive edge over Ready-mix competitors. You will be able to deliver highly accurate fiber-reinforced concrete mixes, even in remote locations. Plus, the concrete you pour will be fresh and ready for your project exactly when it is needed. As with all volumetric mixers that can produce fiber-reinforced concrete, only polypropylene (fiberglass) fibers can be used in a ProAll Reimer Mixer.
CONCLUSION
Fiber-reinforced concrete has been growing in popularity for several decades now. Whilst scientists and engineers are still looking for the perfect fiber, contractors already have a choice between various types of fibers to suit their specific applications.
Being able to offer fiber-reinforced concrete to your clients increases the range of construction projects your company can bid for. Granted, FRC tends to be about 10-15% more costly than traditional concrete. But the benefits gained from its longevity more than make up for the increased cost.
Adding the fiber feeder to your volumetric mixer is an excellent investment in the future of your business.