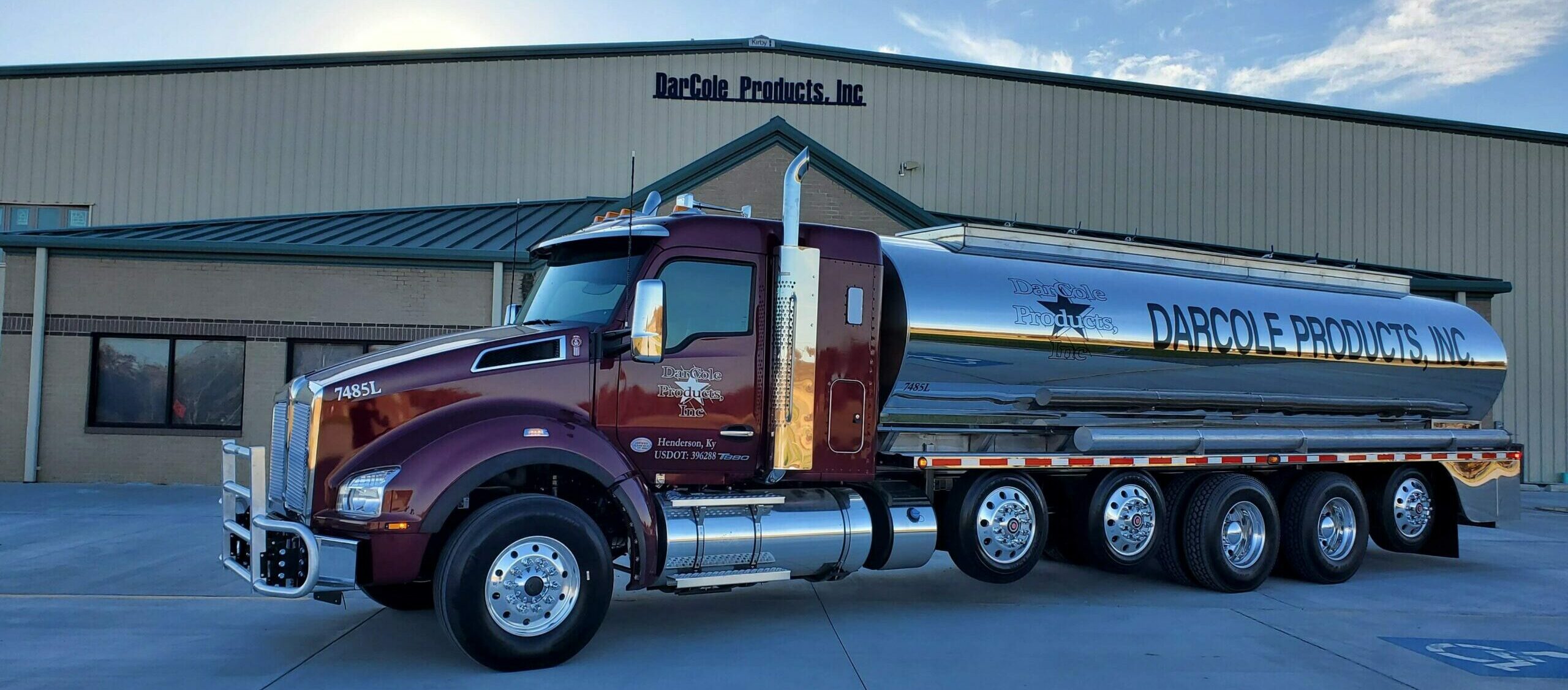
Using Admixtures in Mobile Concrete Mixers
How Does Admix Work in Volumetric Mixers?
Mixing concrete is generally straightforward. Combine the right ratios of water, cement, and aggregate, and you get a highly versatile and cost-effective building material. Its durability, versatility, and cost-effectiveness have made concrete the world’s most widely used construction material. After water, concrete is also the second most consumed material globally.
Volumetric mobile concrete mixers have made it even easier for contractors to deliver high-quality, fresh concrete with every pour. But what happens with more specialist applications, and can volumetric mixers accommodate admixtures? The answer is yes, and you do not just need to take our word for it. Companies all over the world are using admixtures in volumetric mixers to improve their mixes.
We talked to Ryan Risley, Vice President of DarCole Products, Inc. DarCole has been in the volumetric concrete industry for four decades and produces a line of admixtures specifically for use in volumetric mixers.
What Admixtures Add to Concrete
Around the middle of the last century, most concrete was simply made of up cement, aggregate, and water. Today, the majority of all mixes contain admixtures. Admixtures are chemicals that are added to a concrete mix either immediately before or during the mixing process. These substances change the chemical, physical, and mechanical properties of concrete. Depending on their composition, they may influence one or more characteristics of the final mix.
Most contractors have started relying on admixtures to reduce the overall cost of construction projects. Others use admixtures to ensure a continuously high level of quality of their concrete throughout the process of mixing, transporting, pouring, and curing concrete.
ProAll mobile mixers remove some of the concerns commonly associated with pouring quality concrete. There are no delays, and concrete is mixed right before it is poured. That fact has given rise to one of the most common misconceptions in the industry – the long-standing belief that admixtures do not work in volumetric mixers.
Ryan Risley says: “Admixtures in the Readymix industry will not activate for a given period of time or require a certain amount of mix time. In the volumetric application, the admix needs to activate instantly because of the short mix time.”
Shortening the activation time to avoid delays is the key to pouring quality concrete with admixtures using a mobile mixer. Contractors need to ensure they are choosing the most suitable admix for their application.
Common Applications of Admixtures in Volumetric Mixers
Some of the most common admixtures are available in liquid form. Others are only used in very small amounts. These include pigments, pumping aids, and expansive agents, among others. A closer look at the usage of admixtures reveals the versatility of these chemicals.
“We produce four core admixtures that will cover most requirements,” says Ryan Risley. “These four products are our most popular admixtures, but we also offer a full line of specialty admixtures that are generally used in specific jobs. Some of these specific applications include flowable fill (CLSM), shotcrete, waterproofing, dry cast, and corrosion inhibitors.“
Put simply, the company’s range is equally versatile as the volumetric mixers it was designed for.
1. Concrete for Cold Weather Sites
Dealing with extreme climates makes for challenging construction projects in several aspects. Materials react to drastic temperature changes, and persistent frost can put projects on hold for weeks, if not months.
When it comes to concrete mixing and pouring, contractors need to be aware of the time mixtures normally require to set. In temperate climates, concrete tends to be suitable for walking or driving on after 24 to 48 hours. The material reaches its full strength after about four weeks.
In colder climates, contractors may need to accelerate the time it takes concrete to set and develop full strength. Common set and strength accelerator admixtures for colder temperatures contain chemicals like calcium chloride and calcium nitrate. Formates and carbonates also work well in this context.
Frost resistance is another important characteristic of concrete used in colder climates, and air-entraining mixes are ideal for that.
Ryan Risley says: “Our DSA 110 is an air entrainment admixture. Air entrainment creates millions of microbubbles in the concrete that help protect the concrete against cracking due to freezing and thawing. This allows the concrete to expand and contract during a freeze/thaw cycle rather than crack due to movement. The air entrainment also helps with the workability of the mix.”
2. Fast-Setting Concrete
We already touched on the need for accelerated setting times above, and DarCole has developed a specific non-chloride accelerator admixture to support contractors working on jobs where speed is essential: “The DNS 130 speeds up the set time of the concrete. Because it is non-chloride, it will not contribute to any premature corrosion of steel reinforcement in the concrete, and it will not corrode any components on your mixer,” says Ryan.
Acceleration is essential during the winter months or in projects like roadway repairs: “We generally use this in cooler months, or in high early mixes that have a high PSI requirement in a short time. These high early mixes are generally used in precast, or in repairing roadways or parking lots,” Ryan Risley continues.
3. Concrete Requiring Less Water
Water is becoming a scarcer resource around the world, and reducing the amount of water required in construction would be especially useful in areas where water is already in short supply. Water reducers can also make the final material more durable and stronger.
DarCole currently offers several different types of reducers specifically for use with volumetric mixers. Ryan Risley explains: “The DNL 785 is a mid-range water reducer. You can expect around a 10% water reduction with this admix. This water reduction makes the concrete more durable and stronger. In addition, the DNL 785 helps minimize bleed water, improves workability, improves pumping by decreasing line pressure, and coats more cement particles which aid with finishing.”
The company’s DSF 1443 admix is taking water reduction one step further. “The DSF 1443 is a high-range water reducer. It can be used as a multi-range water reducer depending on the application,” says Risley.
“We generally will use this admixture in specialty applications where a low water-to-cement ratio is required. Depending on the dosage, you can expect anywhere from 10% to 40% water reduction. The higher water reduction is crucial for the high early mixes. The DSF 1443 can also be used in precast applications where self-consolidation concrete is required.”
What to Look Out for in Volumetric Admixtures
Ryan Risley believes that best-in-class performance is the key to effective admixture for volumetric concrete mixtures. Without the ability to activate fast, the mixture is simply not suitable for mobile mixers.
“We have a strict quality control program to ensure the uniformity of our products. There are many factors that affect the performance,” Ryan stresses. These factors all contribute to the quality of the finished project, and contractors need to stay on top of a variety of variables.
“The water demand, concrete set times, air content, and overall quality of the concrete are affected by the quality of the raw materials used to make the concrete. Cement, rock, and sand can all affect the performance of your concrete. The admixture reaction for each material can vary, so it is important to run air testing and strength test on all your mixes. The dosage of air can vary due to materials or the geographic location.”
Starting with high-quality, high-performance admixtures is the first step toward ensuring a successful outcome.
How Volumetric Mixers Accommodate Admix
Volumetric mixers simplify the addition of admixtures, no matter how complex a project is. Where admixtures that are only needed in very small amounts, such as pigments, have traditionally been batched by hand, volumetric mixers rely on state-of-the-art technology.
ProAll mixers come equipped with an admixture system that can accommodate two mixes. Each mixer is fitted with two admix tanks, allowing users to pour complex mixes to exact specifications, no matter where their job sites are located. Each ProAll mixer is fitted with the industry-leading Commander control system that simplifies mix design. Operators simply program their desired mix and let the controller take care of the rest.
Programming the control system takes just a few simple steps:
- Calibrate the mixer
- Input the amount of admixture chemicals required per yard or meter
- Start mixing and pouring
The automated system will take care of adding the right amount of chemicals throughout the process. Automation limits the potential for mistakes that could lead to uneven pours or differences in mix design and quality.
Flexibility and Cost-Effectiveness Without Compromising on Quality
Mobile concrete mixers were designed to help contractors deliver the best possible concrete at the right time in the right location. Whether your company specializes in delivering large-scale, remote projects or focuses on small-quantity pours in tight locations, volumetric mixers allow your team to deliver exactly what your customers need.
Ryan Risley sums up the relationship between volumetric and Readymix concrete suppliers: “The most important thing for the volumetric producer is to provide concrete that is as good as or better than the Readymix producer. It is important to provide concrete that is easy to place, and that sets in the proper amount of time. Admixtures are a key component for this because we can help control the set time, and we provide quality concrete that is easily finished.”
Admixtures are becoming ever more common in many concrete applications, including those completed by volumetric mixers. That is why the entire range of ProAll mixers comes readily equipped with a two-product admixture system. This design allows contractors to deliver highly specialized mix designs.
Whether you need to accommodate extreme weather or are simply looking to deliver creative, colorful concrete, admixtures are essential to delivering concrete matching your customers’ specifications. To learn more about how admixtures work in volumetric concrete mixers, contact our team today.