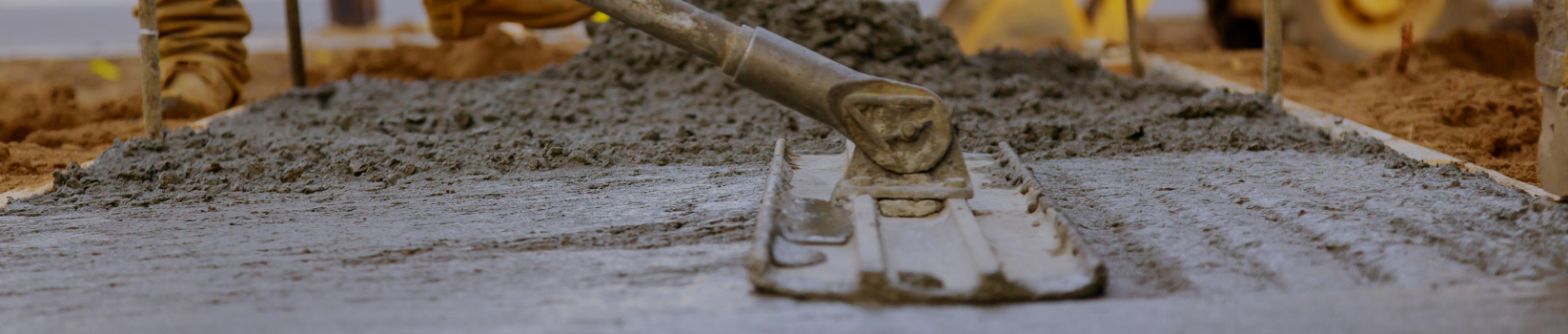
Reducing Waste with Zero-Waste Concrete Mixing: The Volumetric Advantage
Concrete is one of the most widely used materials in construction, but traditional concrete mixing methods often result in significant waste. In an era where sustainability and cost-efficiency are key concerns, businesses seek ways to minimize material waste while maximizing profitability. ProAll volumetric mixers provide a zero-waste solution by allowing precise, on-demand concrete mixing, reducing excess material, and eliminating the need for over-ordering. This blog will explore how ProAll volumetric mixers help reduce concrete waste, save money, and provide a more sustainable construction approach.
The Problem of Concrete Waste
Traditional drum mixers have been the industry standard for decades, but they come with inefficiencies that lead to waste:
- Over-ordering: Ready-mix trucks require batch orders in advance, often leading to excess concrete that is unused and discarded.
- Limited Workability Window: Once mixed, concrete has a limited timeframe before it sets, leading to wasted batches if there are delays on the job site.
- Leftover Material: Any unused concrete in a drum mixer must be disposed of, typically at a landfill, contributing to environmental issues.
- Inaccurate Mix Ratios: Traditional methods rely on batch processing, which can result in inconsistencies, leading to poor-quality pours and potential rework.
The Volumetric Mixing Solution
ProAll volumetric concrete mixers eliminate these inefficiencies by providing a fresh mix on demand. Our mobile batching plants mix raw materials—cement, water, aggregates, and admixtures—on-site, delivering the amount needed without excess waste. Here’s how ProAll volumetric mixers create a zero-waste solution:
1. On-Demand Mixing for Exact Quantities
Unlike drum mixers that require pre-mixed batches, ProAll volumetric mixers allow operators to produce only what is needed. This eliminates over-ordering and excess concrete that would otherwise be discarded. Operators can adjust the mix on-site, ensuring the exact quantity is produced.
2. No Leftover Concrete
Because ProAll volumetric mixers mix materials on-site, there is no risk of leftover concrete setting inside the drum. Any unused raw materials remain separate and can be stored for future use, reducing material waste and disposal costs.
3. Customizable Mix Designs
ProAll volumetric mixers allow precise control over the mix design, making it easy to adjust slump, strength, and other characteristics. This reduces the risk of producing incorrect mixes that would otherwise go to waste.
4. Eliminating Rejected Batches
With traditional drum mixers, there’s no going back once concrete is batched and transported. If the mix isn’t right for the job or conditions change, the batch may be rejected, resulting in wasted material. ProAll volumetric mixers eliminate this issue by allowing adjustments in real-time.
5. Reduced Carbon Footprint
By reducing concrete waste, volumetric mixers contribute to lower CO2 emissions. Less waste means fewer raw materials must be produced, transported, and disposed of, making volumetric mixers a more sustainable option for environmentally-conscious construction firms.
The Financial Benefits of Reducing Concrete Waste
Beyond the environmental impact, reducing concrete waste has significant financial benefits. Here’s how ProAll volumetric mixers help businesses save money:
- Lower Material Costs: Since volumetric mixers only use what’s needed, businesses save on raw materials, reducing unnecessary expenses.
- No Disposal Fees: With drum mixers, leftover concrete often needs to be hauled away and dumped, which is expensive. Volumetric mixers eliminate this expense.
- Less Labor Time and Cost: Operators spend less time dealing with waste, cleanup, and reorders, improving overall job efficiency.
- Higher Profit Margins: By minimizing waste, businesses can complete more jobs with the same amount of raw materials, increasing profitability.
Real-World Applications: Industries That Benefit from Zero-Waste Concrete Mixing
ProAll volumetric mixers are particularly beneficial for industries where precision, flexibility, and efficiency are crucial. Some of these industries include:
1. Utility and Infrastructure Projects
Municipalities and utility companies often require small, precise amounts of concrete for maintenance and repairs. Volumetric mixers provide on-demand mixing without excess waste, making them ideal for roadwork, waterline repairs, and sidewalk maintenance.
2. Remote and Rural Construction
Transporting ready-mix concrete can be costly and inefficient in remote locations. Volumetric mixers allow construction teams to produce concrete on-site without worrying about setting times or material loss during transportation.
3. Commercial and Residential Construction
Builders working on varying project sizes benefit from volumetric mixers’ ability to adjust mix designs on the fly. Whether laying a foundation or constructing a driveway, volumetric mixers eliminate over-ordering and wasted concrete.
4. Shotcrete and Specialty Concrete Applications
ProAll volumetric mixers can adjust water content and additives in real time for applications like shotcrete, ensuring the best results without wasted material.
How to Transition to a Zero-Waste Concrete Operation
If you’re considering reducing waste and improving efficiency with volumetric mixers, here are a few steps to make the transition:
- Assess Your Current Waste Levels: Evaluate how much concrete waste your business generates and calculate potential savings with a volumetric system.
- Invest in the Right Equipment: Choose a volumetric mixer that meets your project needs and capacity requirements.
- Train Your Team: Educate operators on using volumetric mixers effectively to optimize efficiency and reduce material waste.
- Monitor and Adjust: Track material usage and refine mix designs to achieve the best balance between efficiency and quality.
Volumetric concrete mixers offer a game-changing approach to reducing waste in the construction industry. By mixing only what is needed, eliminating leftover material, and providing on-the-fly adjustments, volumetric mixers create a more efficient, cost-effective, and sustainable method for concrete production. Whether you’re a contractor, municipality, or business looking to cut costs and reduce environmental impact, transitioning to volumetric mixing is a wise investment in the future of construction.
Are you interested in learning more about how ProAll volumetric mixers can help your business achieve zero-waste concrete production? Contact us today to explore our innovative solutions!
Cut Waste, Save Money, and Build Smarter with ProAll Volumetric Mixers
Stop over-ordering and eliminate wasted concrete with on-demand, precision mixing. ProAll volumetric mixers give you complete control over your concrete production, saving you time, money, and materials. Take the next step toward zero-waste construction today!