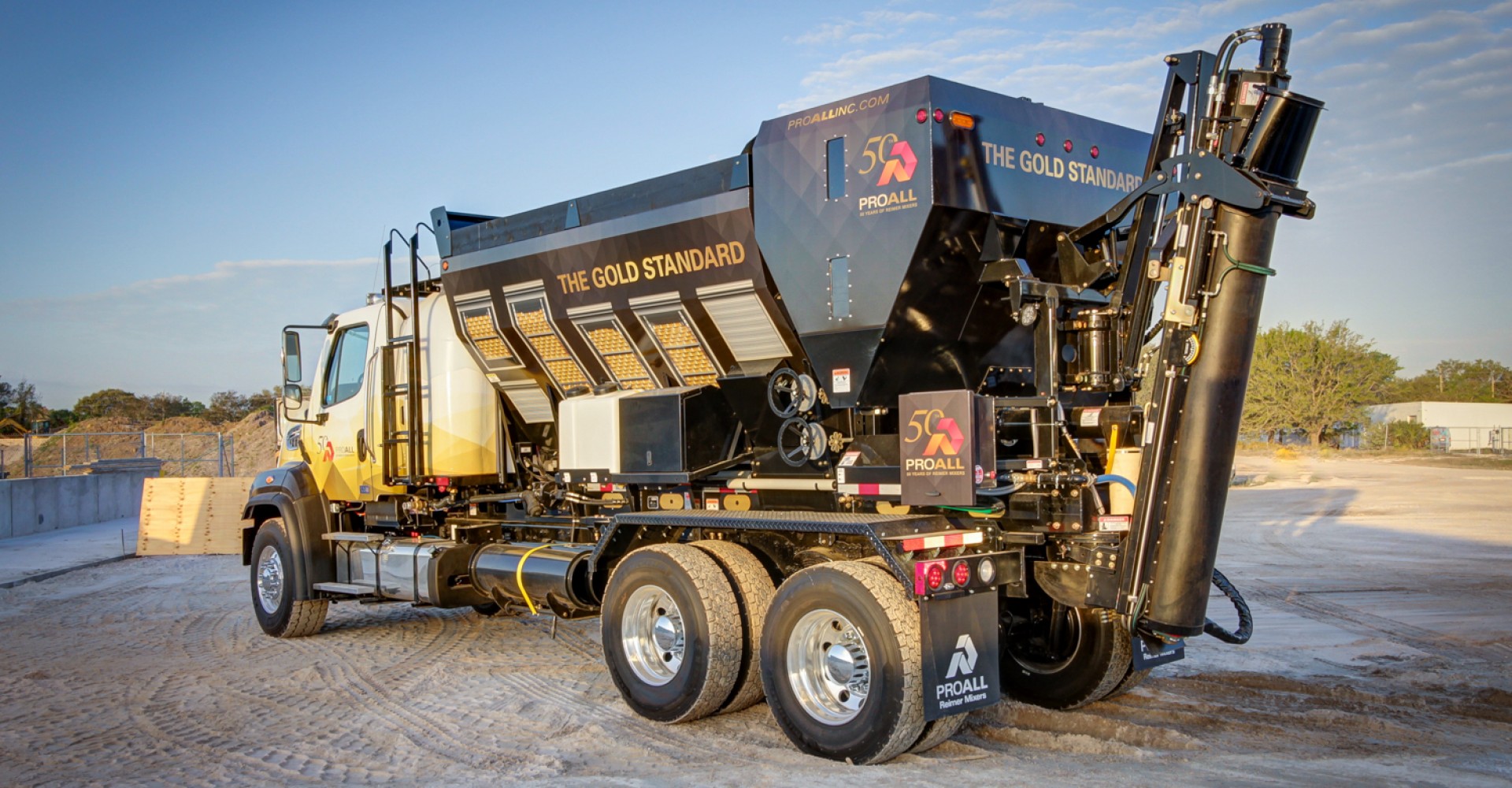
HOW DOES A VOLUMETRIC MIXER WORK?
HOW DOES A VOLUMETRIC MIXER WORK?
Volumetric mixers have been around Canadian construction sites for decades. Contractors started using them in the 1960s. However, far from being old news, volumetric mixers are the future of high-quality concrete delivery. Here is a closer look at their history and the technology that drives them today.
A LITTLE BIT OF HISTORY OF REIMER MIXERS
The concept of mixing concrete by volume dates back to the Roman Empire. As the legions advanced across Europe, builders were not far behind. Mixing construction materials by volume rather than weight allowed them to move their construction wherever the conflicting armies had caused damage.
The build of the Panama Canal also relied on volumetric concrete mixing. More than 4.5 million cubic tons of concrete were needed over several years to build locks and other structures.
Neither of those had the advantages of an automated volumetric mixer. The earliest design for a volumetric mixer came from Daffin Mixers sometime in the late 1950s in Europe. These mixers were then imported to North American and in the 1960s several manufacturers began designing their own versions.
At this time, the Reimer family created their own version of a volumetric mixer in Ontario, and by 1962, volumetric mixers were becoming a common sight around construction sites. The original technology, whilst offering flexibility, remained basic. Adjusting the exact mix could be tricky for the operators.
Since then, technological developments have made mixers more versatile. In the 1970s, contractors started using concrete modified with latex to use as an overlay on bridge decks. When the standards for this type of concrete work were written, they specified volumetric mixers as the approved method of production.
Next came the 1980s and with them an explosion of smaller do-it-yourself construction projects. Smaller amounts of concrete were in high demand. Volumetric mixers were the ideal piece of equipment to provide just the right amount of concrete on several construction sites in different locations on the same day.
The short loads provided by ProAll Reimer mixers meant that homeowners could easily build a patio or make that small improvement they had been considering for years.
Volumetric mixers were even utilized by several branches of the military during the Gulf War. In the 1990s, demand increased once more as rapidly hardening concrete became the material of choice for highway projects towards the end of the decade.
In 2021, almost 60 years after volumetric mixers were first invented, technology has changed the face of the construction industry. Automation has not only made it easier to achieve the perfect mix every time, but it has also allowed volumetric mixers to operate much more efficiently. Comparing pictures of a 1962 Reimer mixer and a 2020 ProAll Reimer mixer makes those differences obvious.
BASICS OF VOLUMETRIC MIXERS
A volumetric mixer can sit on almost any truck bed large enough to take the weight and size of the machinery. Right behind the cab sits the mixer’s water supply. Complete with its own onboard water pump, it carries enough water for mixing and for the clean-up process.
Behind the tank, taking up the largest part of the truck bed, sit two aggregate bins side by side. The bins are open, allowing easy refill for continuous pour systems. Internal bracing ensures the bins’ high structural integrity. At the back of the truck bed sits a large, enclosed cement bin. Its sizable lid allows opens easily and makes loading possible from individual cement bags or overhead silos, depending on the quantity needed for the job.
These obvious parts are not dissimilar from the 1960s mixers, even though the design has changed. Technological changes have affected the measuring, metering, and dispensing of raw materials. Both bins feature individually adjustable flow control gates at the rear of each bin. Those ensure that the correct amount of sand and stone is delivered to the mixing auger, to meet the requirements of the specific mix.
A conveyor belt sits at the base of the bins, on top of a roller chain. This rigid, yet smooth setup forms the base of the belt which delivers aggregate and cement to the mixing auger.
A cement meter at the back of the cement bin controls the amount of cement that is dispensed through the metering auger. Cement agitators help control the flow and create consistency throughout the feed. ProAll mixers introduce water in the mix bowl, just as aggregates and cement enter the mixing auger. A simple control mechanism allows operators to adjust the slump as the ingredients enter the mixing auger.
The auger itself sits at the very back of the truck. ProAll’s mixing augers are capable of delivering concrete at high speeds. They are also fitted with flight cut-outs and additional mixing paddles to ensure a complete mix.
INTELLIGENT FEATURES
Arguably the most important part of the ProAll volumetric mixers is the Commander Control System. The Commander is our flagship control system, and it is one of the main features that sets us apart from our competitors within the industry. Changing mixes and adjusting the speed of the pour can all be done at the touch of a button. Digital control panels and automated functions mean that the operator has more control than ever before. With the Commander Control System, all components of your mix are continuously measured to ensure that every unit of concrete poured meets the exact specifications of every job.
ProAll mixers are packed with additional features. The two-way wireless, digital remote makes the mixer (almost) as simple to operate as a smart TV. One operator can start and stop production and adjust the mix. There is no need for a three-man team. As a result, contractors can use their employees as efficiently as possible.
Some of the top benefits of a modern volumetric mixer revolve around automation. The automated water system means the operator can be sure the exact amount of water required for the selected mix is added. However, the manual override system allows for adjustments by the operator if required.
Automation also ensures each yard of concrete receives the exact amount of admix chemical required per yard. All you do is calibrate the mixer, input how much of the chemical is required, and the Commander control system takes care of the dosage.
All ProAll mixers are equipped with variable speed adjustment capabilities. Operators input the amount of concrete they require of a certain mix, and the metering auger automatically makes the adjustments. No need for recalibration or a manual gear change between mixes.
BEYOND ONE SIZE FITS ALL
At ProAll, we pride ourselves on more than 50 years of innovation and advancement in mixer product design. Just like no two construction projects and concrete pours are the same, we understand that different projects require different mixers.
The ProAll P50 is one of our smallest models but still delivers the same throughput as a larger model. Our designers created it for a shorter, wheel-based chassis allowing it to operate with the smallest footprint among the high-production models in the fleet. The P50 comes into its own in tight spaces like city streets where contractors need to optimize every single meter. Despite its small footprint, the P50 can pour 60 cubic meters per hour.
On the other end of the spectrum sits the ProAll P95. Our largest and most robust mixer comes into its own when your projects demand high-volume production capacity. Large-scale jobs, long-term projects, remote locations – the P95 was made for those. The P95 Trailer takes the concept one step further. Think of it as a portable, volumetric plant. You pull it to the job site, set it up, and don’t have to worry about delays in concrete pours again.
Most contractors’ projects are likely to fall somewhere in between these two extremes. That is why we designed the P75 and the P85 models. High-volume production and specialist applications are part of what these mixers deliver. The P75 has been streamlined and comes with fewer bells and whistles, but with an outstanding price point. For those who need an allrounder with all of the automation features, the P85 has become the mixer of choice.
Volumetric mixers are all about versatility and customization.
UNBEATEN COST-EFFECTIVENESS
Compared to Readymix trucks or batch plants, volumetric mixers deliver better value for money for a wide range of applications.
If your project requires slow pours or concrete is needed only intermittently, a ProAll Reimer mixer ensures that your concrete is fresh every time it is poured.
Smaller projects that need less than a full load often lead to large amounts of wasted concrete. With a volumetric mixer, there is no need to mix any more than you need to pour. The same is the case for balance or cleanup loads.
Few construction sites are conveniently located next to a batch plant. Instead, the already mixed concrete needs to travel long distances. Not only can this cause delays and inconvenience, but it also affects the quality of your concrete. Sitting on hot, sunny highways means water will evaporate from your mix. To make the concrete usable once it arrives at the site, water needs to be added. This lessens the integrity of the final mix.
Remote sites are the extreme application of this same concept. Delivering materials to remote construction sites regularly causes delays. Being able to mix concrete on-site, when you need it, and in the right quantity and quality is preferable.
Towards the end of a project, or when contractors are working in public spaces, after-hours work is normal. After-hours concrete deliveries are costly. A volumetric mixer avoids those costs, and you will never be in a situation where you run out of concrete at a time when it is impossible to order more.
UNBEATEN MIXES AND CUSTOMIZATION
Volumetric concrete mixers give you back control over your project.
If the cement to water ratio is critical, operators can ensure they get exactly what they require. Plus, adjustments are easily made on-site before any concrete has been wasted. Sprayed concrete applications like gunite and shotcrete often adhere to surfaces better than regular concrete. Water content is crucial, and there is really no alternative to mixing on-site.
Low-slump mixes like pervious concrete and roller-compacted concrete are generally more successful with volumetric mixers. The same can be said for high-slump mixes such as floor toppings.
Any time your projects require specialty concrete is the perfect time to consider a volumetric mixer. Volumetric concrete mixers shine on utility projects that use Fast Set Flowable Fill and Rapid-Set Concrete.
Customization of mixes and applications is one of the strengths of ProAll Reimer mixers. Whether your site requires flowable fills or backfill after an excavation is finished, volumetric mixers can help with soil stabilization.
What’s more, there is no need to throw away old concrete. Depending on the specific mix your project requires, old concrete can be recycled and used as part of the aggregate.
THE FUTURE OF CONCRETE
Volumetric concrete mixers are the future of construction. Their versatility will allow contractors to bid for a larger variety of jobs as the equipment simply scales up and down as required. The same versatility will help make specialty mixes easier to deliver than ever before.
The true key to the future of concrete, however, is technology. Just like it revolutionized what volumetric mixers can do between 1960 and 2021, technology will continue to advance this industry. Project diagnostics, data logging, advanced hydraulics, automated production, and even fleet management are already part of the service offered by premium manufacturers.
To help the industry retain high standards now and ensure those will be kept for the future, leading volumetric mixer manufacturers joined forces in 1999 to form the Volumetric Mixer Manufacturers Bureau (VMMB). Standards, testing, and safety are the VMMB’s focus areas.
By combining industry-leading standards with a commitment to advancing technology and continuously improving the capabilities of volumetric mixers, they will remain the tool of choice for versatile construction.