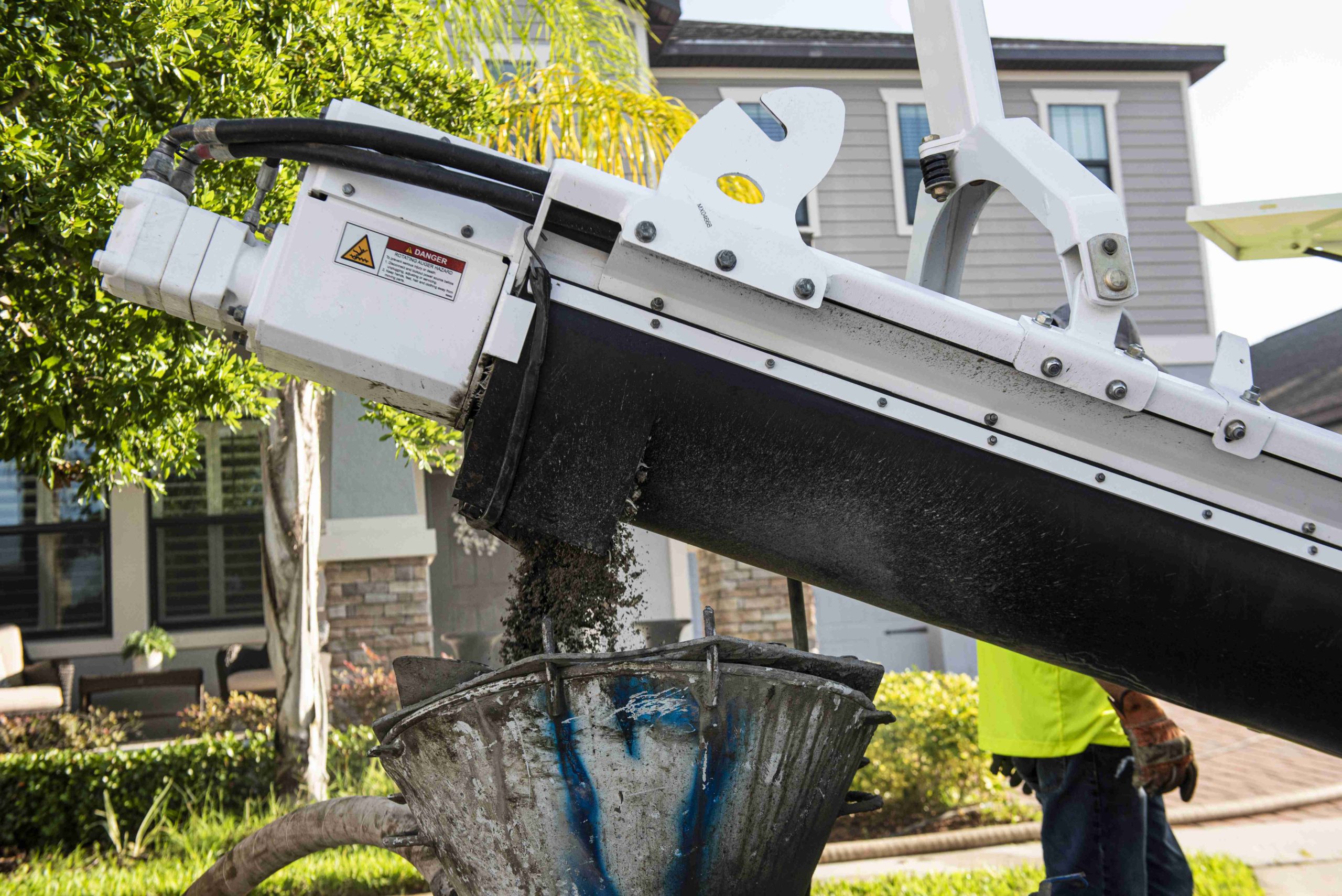
FIVE BENEFITS OF USING VOLUMETRIC CONCRETE MIXERS
FIVE BENEFITS OF USING VOLUMETRIC CONCRETE MIXERS
Getting the concrete just right is the key to success for most construction projects. It is also often more of an art form than a science and relies on experience, and a bit of luck. Volumetric concrete mixers allow you to take the guesswork out of the pour, save money, and minimize waste.
The technology of volumetric mixing has been around for a while, but recent automation has taken it to a new level. Automation like ProAll’s Commander Control System makes mixing more accessible and more precise.
This precision is vital for the strength and durability of the concrete you are pouring. Concrete is commonly used as the foundation for large buildings and other structures. Its integrity is crucial to the lifespan of the structure. Concrete is also one of the most cost-effective building materials. It is safe, doesn’t burn, rot or rust, and is unbeaten for its versatility.
Volumetric mixers deliver on all those and have several advantages over Readymix.
- On-Site Concrete Mix Control
- Quantity Control And Cost Savings
- Speed Of Pouring
- Perfect For Remote Locations
- More Sustainable
1. ON-SITE CONCRETE MIX CONTROL
Using a volumetric concrete mixer puts you back in control right on the construction site. Your concrete will be fresh and exactly the right degree of slump. There is no need to accept whatever quality of mix comes out of the concrete drum.
If your project requires strong, dry concrete, you simply adjust the mix by adding less water. Changing the consistency of the material is as easy as using a touchscreen. Therefore, you can use your workforce more effectively.
Hiring Readymix trucks means your business is effectively using three people: a truck driver, a batch operator, and a load person. With an automated volumetric mixer, no specialist concrete knowledge is required. One person simply programs the required mix into the controller, and you’re ready to pour.
2. QUANTITY CONTROL AND COST SAVINGS
Trucking in ready mixed concrete might seem convenient but it is hard to gauge exactly how much you need. Granted, experienced project managers are able to estimate quantities well. However, an estimate is never as precise as it is to start and stop pouring when you need to.
Smaller projects benefit especially. Not every construction site needs a full truck’s worth of concrete. By using a volumetric mixer, you mix to your requirements and there is no need to pay for a full truckload. Alternatively, if you need to supply concrete to different sites, a volumetric mixer can travel between those.
Mixes can easily be adjusted between sites with a few adjustments on the touchscreen of the commander control system.
Using a volumetric mixer minimizes operational costs on every project. Producing your own concrete on-site can save up to 40%. Project costs will drop, and the initial investment into the volumetric concrete mixer can generally be recovered in less than five years.
3. SPEED OF POURING
Unexpected delays are one of the biggest problems in any construction project. They soon add up to put the whole job behind schedule and lead to additional costs. Ideally, you want to start pouring concrete as soon as the form is finished.
Waiting for a new batch of concrete is a thing of the past if you have your own mixer ready on-site. Your team can easily see when concrete is needed and how much of it. You avoid waiting around for the next delivery.
In addition, your site is never blocked by an endless line of trucks cueing up to deliver to you. No time is lost on-site, and the project progresses more smoothly. Staying on track is an excellent way to impress your clients, increase your credibility, and encourage repeat projects.
4. PERFECT FOR REMOTE LOCATIONS
Deploying large quantities of concrete in remote locations is challenging. Relying on Readymix trucks can easily create a bottleneck. Moreover, if the trucks are stuck on the road in a hot environment, you may have to add water to the slump to make the mix workable again. As a result, your mix is weaker.
Volumetric mixers allow you to transport the ingredients on the truck but in separate bins until you are ready to mix and pour. The mix will be exactly what the project requires.
Large jobs can be handled by one or two volumetric mixers if you create a continuous flow system. Material bins are steadily refilled as the mixer pours. The automated control system ensures that the mix is exactly what you need, and the refills ensure there is no need to stop until you are ready to.
You avoid a long supply line or having to set up a temporary batch plant, adding convenience to even more cost savings.
5. More Sustainable
Not only is using volumetric mixers cost-effective, but it is also good for the environment. Mixing only what you need reduces concrete waste. Especially when building far away from the plant, owning a volumetric mixer avoids long travel times and the repeated journeys Readymix trucks would need to make.
Plus, you can recycle materials in your mix. Demolished concrete and latex paint are only two of the materials that can be reused. The latex can help create a dense mix that does not require defoaming to remove air. It’s another way of saving time and costs at a site.
THE NEXT STEP
Are volumetric concrete mixers the future of construction? We believe so. The advantages are obvious: easy handling, convenient logistics, and cost savings will all benefit your project’s bottom line and help your business grow.
Interested in taking advantage of the opportunities in volumetric concrete? Visit Our Mixer page to view our full lineup or Contact Us for a quote!