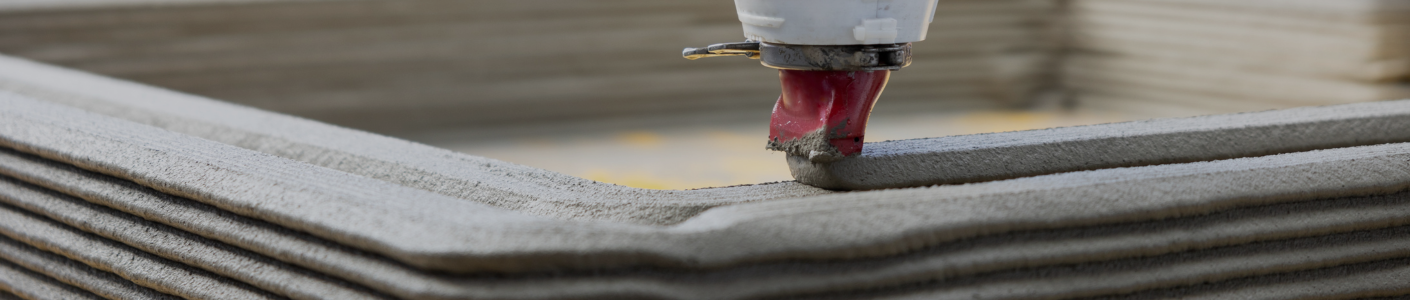
3D Concrete Printing with a Volumetric Concrete Mixer: The Future of Construction
The construction industry is rapidly evolving, and one of the most exciting innovations in recent years is 3D concrete printing. This cutting-edge technology is revolutionizing how buildings, infrastructure, and even homes are constructed, offering speed, efficiency, and sustainability advantages over traditional methods. However, one of the biggest challenges in 3D concrete printing is ensuring a consistent and precisely controlled concrete mix—this is where volumetric concrete mixers come in.
Volumetric mixers provide on-demand, customizable concrete with unparalleled precision, making them the ideal choice for 3D printing applications. In this blog, we’ll explore how 3D concrete printing works, the benefits of using a volumetric mixer for this application, and why this combination is shaping the future of construction.
What is 3D Concrete Printing?
3D concrete printing, also known as additive manufacturing for construction, involves layer-by-layer deposition of concrete through a robotic system or a gantry-mounted printer. The process eliminates the need for formwork and allows for rapidly constructing complex structures with minimal waste.
How It Works
- Digital Design – A 3D model of the structure is created using specialized software.
- Material Preparation – A high-performance concrete mix is formulated to have the right consistency and workability.
- Layered Printing – The 3D printer extrudes the concrete mix layer by layer, following the design precisely.
- Curing and Strength Development – Like traditional concrete, the printed structure gains strength over time.
The Role of Volumetric Concrete Mixers in 3D Printing
For 3D concrete printing to be successful, the mix needs to be precisely controlled, with the right flowability, setting time, and strength. A volumetric concrete mixer offers significant advantages over traditional batch plants for this application:
1. Precise Mix Control
Volumetric mixers allow for real-time adjustments to the concrete mix, ensuring consistency and setting time are perfect for 3D printing. This flexibility is essential for maintaining the flowability required for extrusion.
2. On-Demand Mixing for Continuous Printing
Unlike traditional batch plants, which produce large volumes of concrete at once, a volumetric mixer can produce concrete on demand, eliminating material waste and ensuring a continuous, uninterrupted printing process.
3. Customizable Mix Designs
Different 3D printing projects require different concrete formulations. Volumetric mixers allow contractors to adjust the mix design on-site, adding accelerators, retarders, or fibers as needed.
4. Reduced Material Waste
Because volumetric mixers produce only the required concrete, they significantly reduce waste. This aligns with sustainability goals and helps lower costs.
5. Enhanced Sustainability
By using local materials, minimizing waste, and optimizing the mix for lower cement consumption, volumetric mixers contribute to a more sustainable construction process.
Why Volumetric Concrete Mixers Are the Best Choice for 3D Printing
The advantages of volumetric concrete mixers for 3D printing applications go beyond just convenience. These mixers provide control, efficiency, and cost-effectiveness that traditional methods simply can’t match.
Consistency and Quality Assurance
Volumetric mixers eliminate inconsistencies in the concrete mix, ensuring each layer in the 3D printing process adheres properly and cures correctly. This reduces material failures and enhances structural integrity.
Adaptability to Project Needs
No two 3D printing projects are the same. A volumetric mixer provides the flexibility to adjust mix designs instantly, catering to each structure’s specific strength, workability, and setting time.
Lower Costs and Higher Profit Margins
Traditional batch plants require pre-mixed concrete, which can result in material waste and additional transportation costs. With volumetric mixers, contractors can produce the exact amount needed, lowering material costs and increasing profitability.
Faster Project Completion
Because volumetric mixers can deliver continuous, fresh concrete, the 3D printing process remains uninterrupted, allowing for faster completion times and greater project efficiency.
Check out this video of Premier Gunite using a ProAll Volumetric Mixer to 3D print housing.
Applications of 3D Concrete Printing with Volumetric Mixers
The combination of 3D concrete printing and volumetric mixing is transforming various sectors of construction:
1. Affordable Housing & Disaster Relief
- Faster construction of homes for low-income families.
- Emergency shelters in disaster-stricken areas.
- Reduced costs compared to traditional methods.
2. Infrastructure & Public Projects
- Rapid construction of bridges, tunnels, and retaining walls.
- Custom-designed urban structures like benches, bus stops, and pavilions.
3. Custom Architectural Elements
- Unique façades, sculptures, and artistic structures.
- Complex geometries that would be difficult or impossible with traditional formwork.
4. Military & Remote Construction
- On-site concrete production in remote locations.
- Quick-deployment structures for military bases and emergency response units.
The Future of 3D Concrete Printing and Volumetric Mixing
As both 3D printing technology and volumetric mixing continue to advance, their combination will unlock new possibilities for the construction industry. Key developments on the horizon include:
1. Improved Concrete Formulations
- Self-healing concrete that extends the lifespan of printed structures.
- Lightweight, high-strength mixes for advanced applications.
2. Increased Automation and AI Integration
- Smart volumetric mixers that automatically adjust mix designs based on real-time data.
- AI-powered 3D printing robotic arms for more precise extrusion.
3. Sustainable Innovations
- Integration of recycled materials into 3D-printed concrete.
- Use of carbon-capture technologies to reduce environmental impact.
3D concrete printing and volumetric mixing are a match made in construction heaven. The ability to precisely control mix designs, produce concrete on demand, and reduce waste makes volumetric mixers an ideal solution for this rapidly growing sector. As the technology continues to advance, we can expect to see faster, more cost-effective, and more sustainable construction methods that redefine the way we build.
Are you interested in learning more about how ProAll volumetric mixers can be used in 3D concrete printing applications? Contact us today to explore how our mixers can help you take advantage of this groundbreaking technology.
Build Smarter with 3D Concrete Printing
Unlock the power of on-demand, precision concrete mixing for your next project.