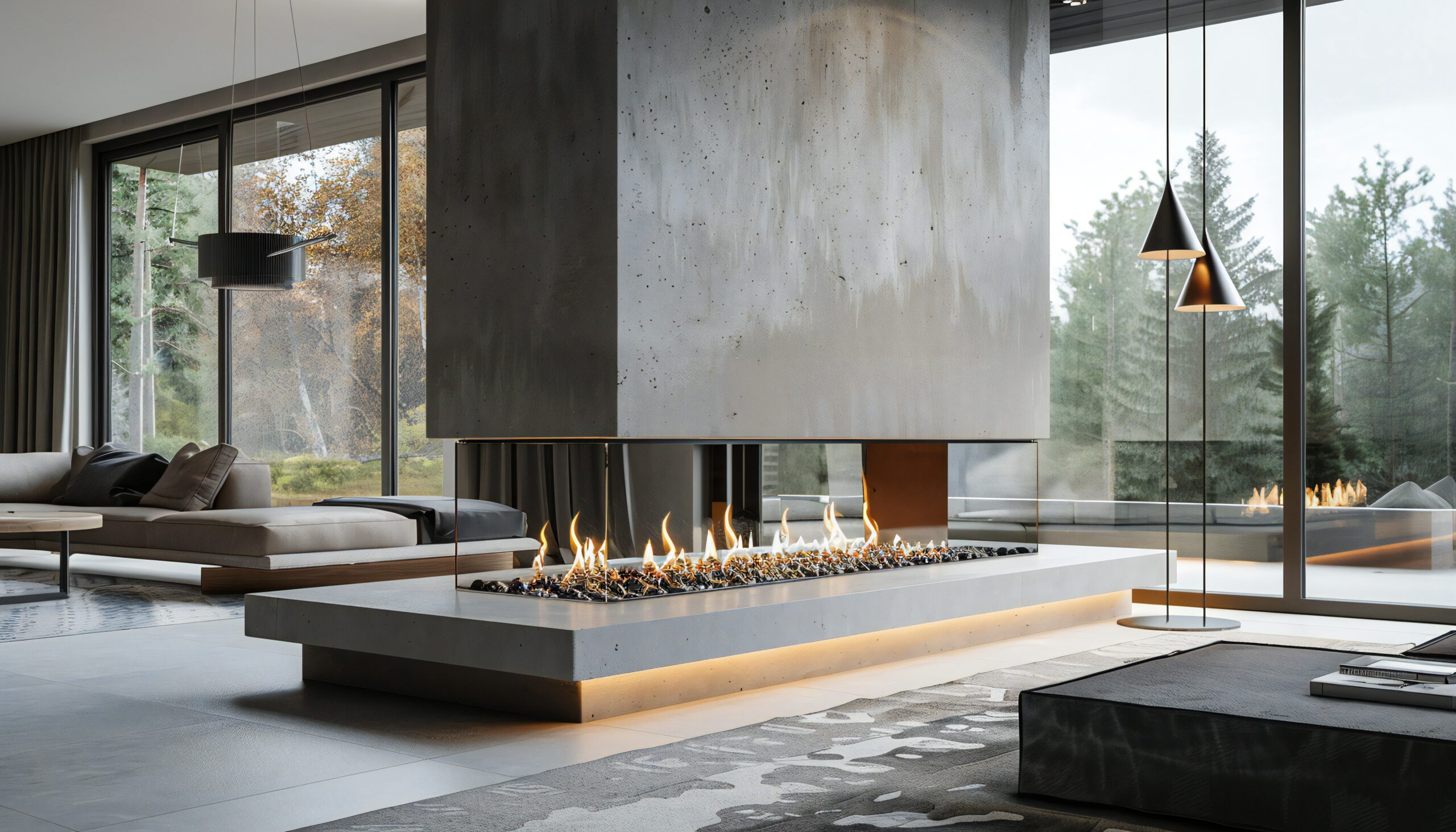
Exploring the Advantages of Heat Resistant Concrete
Concrete is one of the most versatile and widely used construction materials in the world. Its durability, strength, and affordability have made it the backbone of modern infrastructure, from buildings and roads to bridges and dams. However, when exposed to extreme heat, traditional concrete can lose its structural integrity. This is where heat-resistant concrete comes into play, offering a solution for construction projects that demand higher levels of fire resistance and thermal endurance.
In this article, we will dive into the advantages of heat-resistant concrete, its applications, and why it’s a crucial innovation in modern construction. We’ll also explore how volumetric mixers, like those produced by ProAll, are key to creating heat-resistant concrete with the exact specifications needed for various industries. Whether you are involved in the construction of industrial plants, power stations, or simply want a safer and more durable solution for building, heat-resistant concrete may be the answer you’ve been looking for.
What is Heat-Resistant Concrete?
Heat-resistant concrete, also known as refractory concrete, is designed to withstand high temperatures without compromising its structural integrity. Traditional concrete is vulnerable to damage when exposed to temperatures above 300°C (572°F). At this point, it starts to lose its strength, crack, and spall, which can lead to structural failure. Heat-resistant concrete, on the other hand, can endure much higher temperatures, making it ideal for use in environments where extreme heat is a factor.
The key to heat-resistant concrete lies in its specialized mix of aggregates, cement, and other additives. These materials help the concrete maintain its stability even when subjected to temperatures as high as 1000°C (1832°F) or more. This enhanced resilience is what sets it apart from regular concrete and allows it to be used in a wide range of heat-intensive applications.
Key Ingredients in Heat-Resistant Concrete
To understand the advantages of heat-resistant concrete, it’s important to first look at what makes it so different from traditional concrete. Below are some of the key ingredients that give heat-resistant concrete its unique properties:
- High-Alumina Cement (HAC): This type of cement contains a high percentage of alumina, which makes it highly resistant to heat and fire. HAC is often used in the production of heat-resistant concrete because it can withstand temperatures above 1000°C.
- Specialized Aggregates: Heat-resistant concrete uses specific aggregates that don’t degrade under high temperatures. These can include materials like crushed firebrick, alumina, or other refractory materials that have a high melting point.
- Silica Fume and Fly Ash: These are often added to improve the thermal stability of the concrete. Silica fume increases the material’s density, reducing the chances of cracking under extreme heat. Fly ash can improve the concrete’s resistance to thermal shock and reduce the risk of spalling.
- Calcium Aluminate Cement (CAC): CAC is another alternative used in heat-resistant concrete, known for its ability to withstand very high temperatures and for its resistance to chemical corrosion.
Benefits of Heat-Resistant Concrete
1. Enhanced Fire Safety
One of the most significant advantages of heat-resistant concrete is its ability to enhance fire safety in buildings and structures. In fire-prone environments, such as industrial plants or power stations, heat-resistant concrete can be the difference between a minor fire incident and a catastrophic structural failure. Traditional concrete exposed to fire can crack and break apart, allowing fire to spread more easily. Heat-resistant concrete, however, maintains its integrity, providing an additional barrier against the spread of flames.
2. Durability in Extreme Conditions
Industries such as steel production, petrochemicals, and glass manufacturing rely on high-temperature processes. The equipment and facilities in these industries are subjected to extreme heat daily. Regular concrete wouldn’t be able to handle such conditions for long periods, but heat-resistant concrete can. It ensures that industrial plants and their supporting infrastructure remain durable and safe, even under constant exposure to heat.
3. Reduced Maintenance Costs
The durability of heat-resistant concrete means fewer repairs and less frequent maintenance. Traditional concrete exposed to high temperatures will often need to be replaced or repaired, which can be costly and time-consuming. In contrast, heat-resistant concrete can significantly reduce the frequency of maintenance, leading to cost savings in the long run. The initial investment in heat-resistant concrete may be higher, but its long-term benefits far outweigh the costs, especially for industries where downtime is expensive.
4. Prevention of Spalling
Spalling occurs when moisture trapped within the concrete expands due to heat, causing the surface to crack and break apart. This is a common problem in traditional concrete when exposed to fire or high temperatures. Heat-resistant concrete is formulated to resist spalling by either containing less moisture or using ingredients that don’t expand as much when heated. This makes it a safer choice in environments where thermal stress is a concern.
5. Versatility Across Applications
Heat-resistant concrete is not limited to industrial use. It has a wide range of applications, including:
- Fireproofing for buildings: It’s an ideal material for fire-resistant walls, floors, and ceilings in both commercial and residential buildings.
- Furnaces and kilns: Heat-resistant concrete is commonly used in the construction of furnaces, kilns, and incinerators where extreme heat is a constant factor.
- Power plants: The high temperatures in power plants, especially those that use fossil fuels, require materials that can withstand intense heat without deteriorating.
- Fireplaces and chimneys: Homeowners looking to build durable, long-lasting fireplaces and chimneys often turn to heat-resistant concrete for its fireproof qualities.
6. Sustainability Benefits
Heat-resistant concrete can contribute to more sustainable building practices. Because it lasts longer and requires less maintenance than traditional concrete, fewer resources are needed over the lifespan of the structure. Moreover, certain types of heat-resistant concrete can be made using recycled materials, such as fly ash, reducing the environmental impact of the construction process.
The Role of Volumetric Mixers in Heat-Resistant Concrete
Volumetric mixers, like those produced by ProAll, play a critical role in the production of heat-resistant concrete. These mixers allow for on-site mixing of concrete, ensuring that the ingredients are combined precisely and to the exact specifications required for the job. This is especially important for heat-resistant concrete, where the ratio of specialized aggregates, cement, and additives needs to be carefully controlled.
Here are some of the ways ProAll’s volumetric mixers contribute to the production of heat-resistant concrete:
- On-Demand Mixing: Volumetric mixers allow for concrete to be mixed on-site, ensuring that it is fresh and perfectly tailored to the heat-resistant requirements of the project.
- Precise Ingredient Control: The exact proportions of high-alumina cement, specialized aggregates, and other additives can be adjusted with precision, ensuring the concrete has the necessary thermal properties.
- Reduced Waste: Since the concrete is mixed on-demand, there’s little to no waste. This not only saves money but also contributes to a more sustainable construction process.
Industries That Benefit from Heat-Resistant Concrete
Several industries rely heavily on the unique properties of heat-resistant concrete. Some of the key sectors include:
1. Industrial Manufacturing
Factories and plants that deal with high-temperature processes, such as steel and glass manufacturing, benefit greatly from heat-resistant concrete. The durability of the material ensures that furnaces, kilns, and chimneys maintain their structural integrity even under extreme heat.
2. Energy Sector
Power plants, particularly those that use coal or natural gas, require heat-resistant concrete for boilers, chimneys, and other critical infrastructure. The material ensures the long-term stability of the plant, even under constant heat and stress.
3. Petrochemical Industry
Petrochemical facilities often involve high-temperature processing units and require materials that can withstand heat without breaking down. Heat-resistant concrete is used in areas exposed to these temperatures, offering both safety and longevity.
4. Residential and Commercial Construction
While heat-resistant concrete is often associated with industrial applications, it also has a place in residential and commercial construction. Fire-resistant walls, floors, and structural elements made of heat-resistant concrete provide an extra layer of protection, particularly in fire-prone areas.
The Future of Heat-Resistant Concrete in Construction
Heat-resistant concrete is a vital innovation in modern construction, offering enhanced fire safety, durability, and cost savings in a wide range of applications. As industries continue to evolve and place higher demands on materials, heat-resistant concrete will play an even greater role in ensuring the safety and longevity of buildings and infrastructure.
With volumetric mixers like those offered by ProAll, creating heat-resistant concrete has never been easier or more precise. Whether you’re building a fireproof home or an industrial furnace, heat-resistant concrete provides the reliability and performance needed in extreme environments.
By embracing this advanced material, the construction industry can continue to build safer, more resilient structures for the future.
Build for the Heat with ProAll
Upgrade your project with heat-resistant concrete using ProAll’s volumetric mixers. Achieve precise, durable mixes on-site for enhanced fire safety and long-lasting infrastructure. Contact us today to get started!